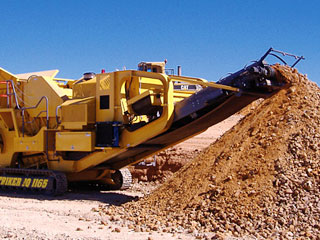
Aggregate and rock crushing operations
Aggregate and rock crushing operations involve the handling and processing of nonmetallic mineral products for the construction industries. Nonmetallic mineral products are quarried or mined and are then transported to the processing plant for further classification and/or further size reduction. In addition, some recycled aggregate products (such as concrete and asphaltic concrete) are also processed in these plants. The processing of sand and gravel for a specific market involves the use of different combinations of washers, screens, and classifiers to segregate particle sizes; crushers to reduce oversized material; and storage and loading facilities. The various types of equipment used in these plants include: hoppers, belt conveyors, screens, scrubbers, pumps, storage bins, crushers, jigs, screws, front end loaders, scrapers, trucks, engines, and generators.
Applications
1. Application requirements any aggregate and rock crushing operation which would emit any pollutant, without the benefit of air pollution control device, greater than or equal to 2 pounds in any 24 hours period.
2. Exemption equipment registered under the portable equipment registration program with carb that is not operated at a permitted stationary source.
3. data forms the following forms must be completed and submitted by the applicant when applying for an authority to construct and/or permit to operate any aggregate and rock crushing equipment (these forms are used by the district to characterize the type of process, size, flow rates, abatement devices, and exhaust stacks of the system):
4. Additional information
- A) Site plan and plot plan, with dimensions, showing location of equipment.
- B) if required because of initial health risk screening, submit a risk reduction strategy. Information needed to evaluate the proposed risk reduction measure(s) shall include, but not limited to — equipment layout with dimensions and location of process equipment; specification of the ventilation system (type of ventilation, rated air flow rate, exhaust stack diameter and stack height), and location of exhaust stack.
Control equipment evaluation
The crushers, screens, and conveyors are all enclosed and vented to baghouses. The baghouses can achieve a control efficiency of 99% and higher for pm10 emissions. The feed hoppers and stacking conveyors drop points are controlled by conventional water sprays, which are expected to achieve a control efficiency of 70-90% (ap-42). Stockpiles at the facility are also controlled with water spray systems, which are expected to achieve a minimum 80% control efficiency (ap-42). Various processes are also thoroughly saturated with water (i.e. Moisture content exceeds 6%). For these processes a control efficiency of 100% is assumed.
Nonmetallic mineral processing plants – because of the type of material and the apc baghouses used on the crushers, screens, and various transfer points, compliance with the opacity limitations of this rule is expected. The NSPS does require the following limitations for the various listed processes:
- A. All process shall be limited to 10% opacity, except as provided in the following.
- B. Fugitive emissions from any truck dumping into any screening operation, feed hopper or crusher shall not exceed 20% opacity or greater.
- C. Fugitive emissions from any crusher, at which a capture system is not used, fugitive emissions which are greater than 15% opacity.