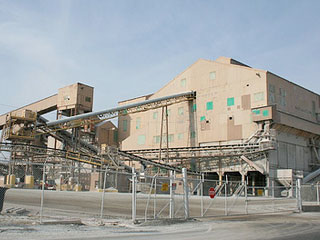
Lime Handling Systems
Lime Handling Systems is a general article dealing with the storage and feeding of lime slurries. Design considerations involved in selection of equipment are discussed in addition to general information on lime.
Recommendations for system designs are discussed with information presented on equipment options.
The article is designed to acquaint the reader with the considerations involved in achieving an efficient and practical lime system.
Detention Slakers-Grinding Mill Type
Grinding mill type detention slakers are best suited to applications where the lime quality is poor, grit handling is costly or when the processing rate exceeds that achievable in a conventional slaker. Grinding mill slakers operate on the same principle as conventional detention slakers, however they have the ability to grind inert materials (grit)contained in the quicklime and generally require little or no grit removal or disposal facilities. Grinding mill slakers are horizontal or vertical ball mills(as commonly used in the mineral processing industry)modified to withstand the temperature of lime slaking. They have the advantage of being relatively simple and rugged. However, grinding mill slakers are the most expensive of the slaker types, have limited capacity for turndown, and consume the most energy.
As shown in Figure 30, a typical grinding mill slaker(horizontal type)consists of a rotating drum supported by external rollers. The mill contains a grinding media(typically steel balls)agitated by means of horizontal lifting bars attached to the interior of the drum assembly. Slaked lime product discharges from the drum and is pumped to a hydrocyclone, which classifies the slurry to recirculate oversize particles to the mill inlet. As with a conventional detention slaker, water to lime ratio in the slaking compartment is adjusted and monitored manually with hand valves and flowmeters.
Grinding mill type detention type slakers are made to order in quicklime slaking capacities up to 60, 000 lbs/hr. Operating parameters and characteristics are similar to conventional detention slakers.
An alternate version of the ball mill is a Vertimill Slaker, which offers significant advantages over conventional Ball Mills. These devices operate vertically and take up minimal floor space, have significantly reduced foundation requirements and can operate over a wide turn down range. A hydrocyclone circuit is not normally required, the lime slaker process is more efficient and produces a finer particle size for increased surface area and reactivity.
Factors Affecting Slaker Selection
Many factors other than price and operating costs will influence the selection of a slaker. Some of the factors are outlined in the following:
Product Quality
Surface area of the hydrated lime product is of paramount importance in many applications. Tests show a correlation between the diameter of slaked lime particles and the water to lime ratio used during slaking. As the water to lime ratio is reduced, the diameter is reduced also, resulting in a substantial increase in surface area of the slaked lime product. Due to the difference in water to lime ratios, paste type slakers deliver more neutralizing capacity(as measured by free base titration)than comparable detention slakers. For certain applications, this difference can result in substantial improvements to the process as well as chemical cost savings.
Grit Disposal Costs
The cost of grit disposal can be a significant factor in the selection of lime slakers. The inert portion of quicklime which is captured by a screen or inclined classifier is relative to the purity and particle size quicklime. This grit must be transferred from the grit removal device to a bin, which is emptied periodically. While the grit itself is not a hazardous material(as defined by EPA), however, the pH exceeds 12. 0 and caution must be exercised in handling and disposal. The grinding mill slaker eliminates the grit disposal problem by grinding the grit to very fine particles, which are carried along with the lime slurry. This type of slaker should be considered where grit disposal costs are high.
Slaking Water Quality
For reliable operation of any lime slaker type, water used for lime slaking should be at a temperature not less than 55°F/12°C. For slakers, which are expected to start and stop frequently, the time to reach operating temperature(with associated hydrated lime quality)may be a factor. Paste type slakers reach their steady state operating temperature in approximately 1/3 rd the time required by comparable detention type slakers. In general, paste slaker performance is less susceptible to cold slaking water (less than 55°F/12°C)than detention and grinding mill slakers. Water heaters may be added to raise the temperature of the slaking water for all types of slakers.
Space Constraints
Like all process equipment, lime slakers require regular cleaning and maintenance. They are often placed within the skirt support structure of the quicklime storage vessel where space is at a premium. The size and shape of the slaker may be a determining factor in slaker selection;in general, paste slakers are the most compact(in plan view). Some conventional slakers are configured with vertical mixing chambers and require less horizontal space, however headroom requirements are greater. For grinding mill slakers, the vertical type require the least space in plan view, however they can be up to 30 ft in height depending on the processing capacity.
Capital Cost
Budget constraints frequently determine slaker selection. Conventional detention type slakers are the least expensive of the three type considered, with paste slakers priced approximately 15%higher for comparable capacities. The higher price of the paste slakers can often be recovered quickly by the more efficient slaking and lower chemical usage. Grinding mill slakers are typically 3-5 times the price of comparable conventional slakers, however this premium can also be offset by the reduction in grit disposal cost.
Operator Experience
The user’s level of experience with lime slaking and prior experience with specific types of slakers should be a factor in slaker selection. For safe and effective lime slaking, operators should have knowledge of the theory and practice of lime slaking. In general, detention type slakers are more forgiving of inaccuracies in lime and water feedrate; however manual slaking water control requires calculation of slaking/dilution water flowrates each time the lime feed rate is changed. In cases where quicklime feed rate is changing frequently, the automatic water proportioning system in paste slakers should be considered. In addition to knowledge of lime slaking, grinding mill slakers require a knowledge of the grinding process and related equipment. For this reason;grinding mill systems require more operator knowledge than conventional slakers and appropriate consideration should be made in the selection process.