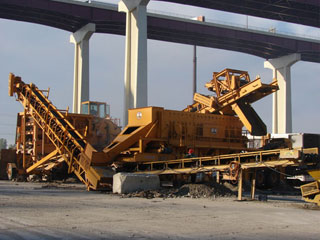
Crushing of hard materials
Crushing of hard Materials
Processes used for crushing hard materials
These processes are used to reduce a material from its original size to a smaller, defined output size.
The main physical size reduction processes are: shattering (breaking) , squeezing, grinding.
Shattering (breaking) is used, as a rule, to reduce materials with grain sizes of >50 mm in size. In squeezing and grinding processes, materials already reduced to grains sizes of 5 50 mm are reduced/ground to extremely small grains. The boundaries between squeezing and grinding are fluid.
Machines used for crushing hard materials
Machines used for crushing hard materials can take materials with edge lengths of up to 2500 mm and reduce them to sizes of a few hundredths of a millimeter in a series of processes. In these machines-crushers, mills and presses-moderately to extremely hard stones, other minerals, coal and sands are processed. Depending on the material and on the desired end product, the following machines may be used:
- Jaw crushers
- Cone crushers
- Hammer crushers
- Roller grinding mills
- Roller presses (cylinder crushers)
- Tube mills
Machines used for crushing hard materials must be characterized by a high efficiency and operational reliability, and they must be easy to maintain. As a leading rolling bearing manufacturer, FAG are making their contribution to meeting these requirements.
Jaw crushers
Principle of operation of double toggle jaw crushers
The jaw crusher was invented in the middle of the 19th century, by an American named Blake. It is also referred to as double toggle jaw crusher.
Double toggle jaw crushers are used as coarse crushers and fine crushers. The principle of operation is intermittent. On a horizontal shaft with an eccentric centre section sits the pitman, which actuates the swing jaw through a double toggle lever system. The swing jaw is supported in sliding sleeves or rubber-bonded-to-metal bondings. Rolling bearings are installed in the pitman (inner bearings) and in the crusher frame (outer bearings) . The crushers feed opening can span more than 2000 mm. The eccentric shaft speed is between 180 and 280 min-1 , depending on the crusher size.
Cone crushers
Principle of operation
Cone crushers, also referred to as gyratory crushers due to their gyroscopic motions during the size reduction process, were developed in the USA, where they were also first built and put into operation.
The Symons brothers contributed considerably to the development of cone crushing machines. The basic principle of cone crushers has remained the same to this day. The principle of operation of cone crushers is continuous, and the crusher axis onto which the crushing cone is mounted revolves at a defined angle to the perpendicular. Depending on the crusher gap adjusted, cone crushers are used either for coarse crushing or fine crushing of materials, effected by the gyratory movement relative to the crusher shell. Cone crushers are designed for large throughputs and are primarily used in mineral processing and in quarries.
The throughput can reach up to several thousand tons per hour, depending on the machine used and on the original size (approx. 8 to 300 mm) of the material to be crushed.
The output size of the crushed material can range from 0 to 70 mm, depending on the crusher size.
Hammer crushers
Principle of operation
Single-shaft and double-shaft hammer crushers have been used for many decades to crush a variety of materials As primary and secondary crushers, they are used for crushing bulk materials, e. g. limestone, marl, coal, gypsum, clay, etc.
Huge hammer crushers in quarries can reduce material with edge lengths of up to 2. 5 m and weighing up to 5 tons to an output size of approx. 25 mm in one single operation. They can reach throughputs of up to 2500 t/h. In single-shaft crushers, the material is smashed against one or several jaw plates by rotating beater works (hammers attached to the rotor) . The rough-crushed material is further reduced in size between the rotating hammers and the grinding tracks. The end product falls through the grid openings in the bottom plate of the crusher.
In double-shaft hammer crushers, the material is first rough-crushed above the rotors and then reduced to their final grain size by the two counterrotating beater works. The end product falls through the grid openings in the bottom plate of the crusher. Hammer crushers work, depending on their size, at speeds ranging from approx. 200 to 2000 min-1 . The required power can be 1000 kW and more.
Roller grinding mills
Principle of operation
Roller grinding mills, also referred to as bowl mill crushers or vertical mills have been used for crushing hard Materials already for many years. Roller grinding mills are used to reduce in size, e. g. limestone for cement production or coal in heating power stations. Various manufacturers worldwide offer roller grinding mills with similar principles of operation.
The material is reduced in size between a driven, rotating plate with a vertical axis, and a number of rollers with differently shaped outside diameters positioned above. The material is fed in over and over until it has been reduced to the specified grain size. The number, form and Arrangement of the rollers vary depending on manufacturer and specific application.
Roller presses
Development and principle of operation
Roller presses, also referred to as cylinder crushers or horizontal mills, were developed in the mid-eighties. They consume considerably less energy than is required for traditional size reduction processes. Machines are currently being developed which will even surpass the throughput of 1000 t per hour generally obtained today. In this connection, FAG maintains a dialogue with all roller press manufacturers of importance. Roller presses are used for coarse grinding, hybrid grinding and fine grinding. Coarse grinding produces grain sizes of up to 20 mm, fine grinding up to 0. 04 mm. Typical grinding stocks include raw material of cement, cement clinker, foundry sand, coal and ores as well as other mineral materials.
One of two rolls which are synchronously driven in counterrotation is hydraulically adjusted against the other one. Under high pressure the roller press causes the formation of cracks in the material charged. Misalignments caused by the grinding process are compensated via the adjustment mechanism of the hydraulically preloaded roller. Depending on the requirements, the rollers feature either a level or a shaped surface.
Tube mills
Principle of operation
Tube mills are heavy machinery which reduce material in size through rotary motions. Essentially, they consist of a horizontal or slighty inclined grinding tube and face covers through which the grinding stock is fed in and discharged. Mills in which the grinding stock is reduced in size by means of loose grinding bodies (balls or rods) are referred to as ball or rod tube mills. “SAG mills” (semi autogeneous grinding mills) operate with a reduced number of grinding bodies.
Autogeneous tube mills (AG grinding mills) are mills which reduce the material in size without grinding bodies.
Grinding stock for tube mills include gold, tin, copper and iron ores as well as coal, limestone and cement.