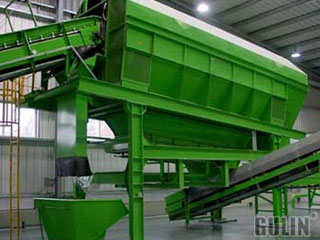
Dry magnetic separation of ilmenite
The deposit for Case Study 1 was a typical aeolian reworked mineral sand deposit with a heavy mineral assemblage of ilmenite, rutile, zircon, sillimanite, monazite, magnetite and other minor minerals.
In Early path finding test work of small samples indicated that a majority (~70%) of the ilmenite could be recovered as finished product by using RED magnetic separators as the first separation step—rather than electrostatic separation as is most common.
To validate this important finding, a single stage magnetic fractionation, using an Gulin® RED equipped with multi-tray collection boxes, was performed. The feed was generated by gravity concentration to >95 % HM and NaOH-based attrition scrubbing. The results are summarized in Table I, substantiating the earlier findings. The results indicate that total ilmenite product from this unit operation would amount to 66% weight of the HMC feed, and the corresponding quality was well within product specifications.
The early tests shaped the larger pilot testing flowsheet, with the essential elements as follows:
- Scalping by low-intensity drum magnet to remove ferromagnetic materials. This magnetic stream was combined with the primary ilmenite product
- Magnetic fractionation by RED to recover 50 to 60% weight of the feed as a primary ilmenite product; requiring no electrostatic pretreatment
- Recovery of residual ilmenite in the RED non-magnetic fractions as secondary and tertiary ilmenite products via retreatment with higher intensity RER followed by cleaning with high tension roll (HTR) separators
- After ilmenite removal, the final non-magnetic stream was subjected to traditional processing methods to generate rutile and zircon products.
A simplified process flowsheet for the ilmenite circuit products is depicted in Figure 4.
A WHIMS was not recommended for this application for the following reasons:
- The presence of garnet and monazite contaminants in the assemblage required electrostatic separation to properly upgrade a portion of the ilmenite product
- Three separate ilmenite products were desired, requiring the flexibility and control that can only be accomplished with dry separation methods
- While rutile and zircon are important products, the production of on-specification ilmenite products was critical to overall project success
- Dry magnetic separation simplified the flowsheet and saved capital and operating costs.