Tantalite processing consists normally of crushing, screening and grinding to liberate the contained mineral in the pegmatite, followed by gravity separation to recover the mineral based on its high specific gravity. The gravity separation techniques used are generally similar to those used for mineral sands (with the exception of conventional jigs), but because of the lower grades, liberation, over grinding and shape factors recovery and concentration is more difficult and usually requires more complex circuits and results in lower recovery and concentrate grade than with the former. Fine particle recovery is a major issue in most situations, and oxide flotation methods have been attempted.
Tin or its ore cassiterite is often associated with tantalite and is recovered using similar methods.
Tantalite processing flow process
Sample analysis & characterization -> Crushing, grinding, screening & classifying -> Gravity separation -> High tension & electrostatic separators -> Magnetic separators -> Flotation
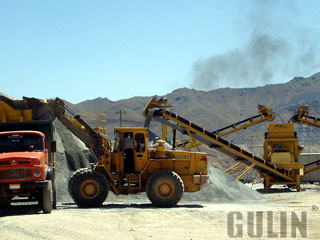
Tantalum & Tin Processing
Sample analysis & characterization
- heavy minerals (tbe sink/float).
- liberation (clerici sink / float & qem.sem).
- mineralogical (microscope identification / grain counting).
- grain size (wet & dry sieving).
- slimes (cyclosizing). • xrf / xrd.
Crushing, grinding, screening & classifying
- jaw crusher (jacques).
- ball & rod mills (various sizes).
- kason screens / derrick screens / trommel / dsm / Gulin screen.
- hydocyclones (krebs / warman / moseley / concord).
- hydrosizers (outokumpu).
Gravity separation
- spirals (various types and makes including roche mt / carpco / multotech ranges).
- closed circuit spiral test rig.
- bulk sample spiral pilot plant for continuous multistage (rougher / cleaner / recleaner / scavenger) operation including automatic sampling at each stage.
- jigs (conventional and kelsey centrifugal).
- mgs separator (pilot size).
- falcon concentrator (bench size).
- wet shaking tables (wilfley ¼ size).
High tension & electrostatic separators
- readings 10 inch roll.
- ore kinetics ultra & corona stat*.
- roche mt single & multistage plate.
Magnetic separators
- readings cross belt & irm.
- eriez re roll & re drum*.
- magnapower re roll & drum.
- improsysre roll.
- readings & eriez whims.
Flotation
- bench & pilot plant flotation cells.
- sulphide (arsenic removal).
- oxide (tantalum and tin recovery).
Facilities & equipment manufacturer
Gulin® provides a comprehensive range of test work capabilities including bacterial leaching, crushing, screening, grinding, ultra fine grinding, gravity, magnetic & electrostatic separation, solvent extraction, electrowinning, flotation, pressure leaching, pressure oxidation, pressure acid leach and cyanide speciation. Pre-feasibility studies, on-site diagnostic metallurgical services, environmental testing and analytical services are also included in our range of capabilities.
The laboratory is dedicated to providing high quality metallurgical testing across the broad spectrum of the minerals industry including: gold ores, nickel laterites, base metal, iron ore, mineral sands, pgm ores, rare-earths and other exotics, diamond ores, environmental services.