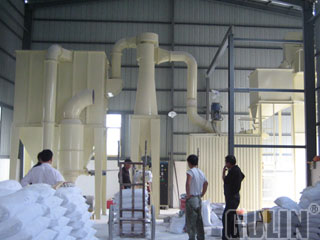
Attrition Grinding Mills
Gulin® is a professional manufacturer and supplier of Attrition grinding mills in China, Our Attrition milling have been used across a wide range of industries and applications, such as paints, pigments, pharmaceuticals, ceramics and coal slurries. It is used to grind limestones, carbonates, talcum. some have classified the ball mill as becoming inside the family members of attrition mills.
Wet attrition milling
Both limestone and water are continuously fed from the top of the mill through a specially designed feed housing. This funnel shaped housing has a cylindrical extension, which projects into the grinding vessel of the attrition mill. The shaft of the mill extends down through the housing and the cylindrical extension with the media agitator arms being disposed just beneath the extension. The rotating shaft utilizes several radially projecting, angled impeller blades, which are within the cylindrical extension. When the shaft rotates, these blades create a pumping action, which forces the limestone and water into the grinding media bed.
Features and benefits of attrition milling
Higher speeds, smaller volumes and higher localized energy concentrations. This mill type was chosen as an example of how mill system advancement, optional mill system arrangements and sparing philosophies can impact overall system design and process effectiveness.
Attrition Milling Process
Attrition milling use media ranging in size from 3mm to 10mm. However, in the wet FGD application, the mill design was altered to incorporate 12.7mm through-hardened carbon steel balls. The specialized mill design allows the 6mm (¼”) feed size of the limestone. Attrition arm tip speed is approximately 270 m/min. After the limestone and water slurry has passed through the grinding media bed, the ground limestone slurry overflows and discharges from the top of the mill into a separation tank. A low speed mixer is incorporated into the separation tank, which allows the fines to continuously overflow to the mill product tank while coarse limestone particles settle to the bottom. A mill recirculation pump then carries the coarse limestone particles back to the mill to be re-ground.