Grinding principle of vibrating mills
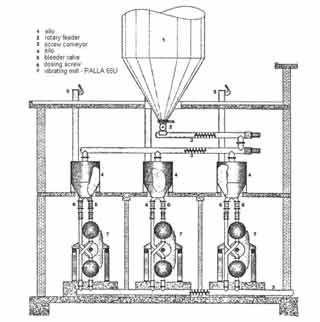
ultra fine grinding circuits
The vibrating mill belongs to the group of mills that make use of impact forces. However, in contrast to the so-called impact mill, the size reduction in vibrating mills is primarily caused by the impact energy of the grinding media rather than by friction or by acceleration of the feed material.
illustrates the vibrating mill with its grinding cylinders, filled up to 65% with grinding media.
Usually rotation impulses of 1.000 min-1 are transferred by the effect of unbalanced weights from the surface of the grinding cylinders to the grinding media, which performs an almost ideal circular movement. Depending on the frequency and the unbalanced mass, an acceleration of several g can be generated (g = acceleration of gravity). The grinding effect is caused by milling the feed material in between the elements of the grinding media and between the elements of the grinding media and the cylinder walls. In addition to the grinding effect based on impact energy, a minor degree of friction forces are generated between the walls and the grinding media, which also leads to a certain size reduction of the feed material. Friction results from the rotation energy of each grinding element and the relative movement of the entire grinding bed against the rotating direction of the unbalanced masses. However, the milling effect is primarily caused by impact and to a minor degree by friction only.
Furthermore a rotation of the entire grinding bed is generated due to the circular movement. Gravity is the driving force of the grinding media. shows the dynamics of an operating vibrating mill.
Three types of grinding media can be used in vibrating mills which, due to their geometry, cause the different impulse transitions:
Rods – linear impact energy Balls – punctual impact energy Cylpebs – linear and laminar impact and friction energy.
Consequently, for achieving an optimal energy transmission, the correct choice of grinding media is essential. For a coarse comminution, friction energy is rather negligible, but gains in importance within the fine zone. Operating with rods, balls or cylpebs as grinding media shows significant differences, particularly in the coarse comminution due to the grinding media’s great difference in mass. Considering these aspects and practical experiences the application range of these three types of grinding media can be set up as follows .
This diagram represents the general trends in media selection. Anyway such as the specific material properties like hardness, density, grain shape, surface properties, etc. have to be taken into account.
For example, with limestone, a certain particle size generates a coating of grinding cylinder walls and grinding media, which negatively effects grindability and transportation within the mill. These coatings mainly occur when milling with balls or cylpebs, where in addition small plates can be formed, which negatively affect the grinding and any downstream air classification. By using rods as grinding media this effect can be avoided and an undisturbed operation can be sustained due to the frequency of the rods. Not only the type but also the size of the grinding media influences the comminution result. Generally the largest grinding element should be able to retract the largest particle in the feed material. But using too big grinding media means decreasing the rating, which again decreases the comminution result. Operating the vibrating mill with too small grinding media, the feed material might pass the mill without size reduction or might accumulate and plug the vibrating mill.
The feed is constantly charged to the grinding cylinders and flows into the gaps of the grinding media via vibration where size reduction and transportation occurs simultaneously. Transportation of material through the horizontal grinding cylinders is based on vibration and displacement of material. The repose angle at the outlet, which controls the throughput, depends on type and size of grinding media, feed size, material properties, and circular motion.
The degree of size reduction depends mainly on retention time and on the throughput.
At the end of the grinding cylinders in-chamber screens can be installed in order to hold back the grinding media in the vibrating mill while the product material is able to pass through.
The following options for the connection of the grinding cylinders for a dry grinding process are possible:
- Series connection
- Parallel connection
- Center feeding.
In these options are shown, the selection of which mainly depends on retention time. Apart from the retention time, the grinding cylinder connection depends on the characteristics of the material so that the presented duration limits may overlap.
Series connection
With this type of arrangement, the feed passes both grinding cylinders successively, which results in maximum grinding path lengths and the longest retention times of >12 minutes. This connection is applicable for fairly hard or coarse feed, for very fine end products, for materials which are characterized by poor blending properties, or for long grinding, dissolving, and reaction processes.
Parallel connection
With this arrangement, either cylinder yields a finished product and shorter retention times of 3–12 minutes and higher throughput rates can be achieved. Identical or different materials can be ground, blended, or chemically treated in the two cylinders at the same time.
This arrangement is suitable for materials that are easy to grind, for closed-circuit grinding, for simple blending operations and dissolving processes, as well as for chemical reactions of short duration.
Centre feeding
In this configuration the material flows in either direction towards the outlet caps. Grinding path and retention time are very short and the throughput is correspondingly high. Size reduction is less than for series and parallel connections. This arrangement is suitable for soft materials requiring minor grinding only or any other substance to reach a product as coarse as possible, for quick chemical reactions, or for dissolving processes.
Estimating the throughput for each material requires milling tests in which different parameters such as frequency, amplitude of vibration, arrangement of grinding cylinders, and grinding media are determined.
Since for most materials the grindability is unknown, milling tests are normally needed prior to the design of a vibrating mill. The optimal design is dependent on the application, product grain size, size distribution, grain shape, and grain surface.
The test works are executed in a small, laboratory-scale, vibrating mill. The results of this test work can be trended and interpolated to any vibrating mill size.
Application in ultra-fine grinding circuits
For over 160 different materials, from soft to very hard, the vibrating mill has been successfully established for grinding, homogenizing, and activating. A high filling degree of the grinding cylinders and a low air throughput appear to be beneficial for materials such as metals, coal, coke, and other organic materials, which tend to increase the risk of dust explosion.
The feed size of a vibrating mill ranges from 0–15 mm (max. 0–30 mm) whereas the product size can be less than 10 μm at continuous operation. In special applications with air classifiers, product sizes smaller than 3 μm can be achieved.
shows an air classifier—vibrating mill circuit. The material is first fed to an air classifier before it is charged to the vibrating mill. This type of circuit is applicable if the feed material contains a lot of fines or significant fraction of the product grain size.
shows a vibrating mill—air classifier circuit, an option frequently applied in the mineral processing industry. A third option operating a vibrating mill process is an open circuit with an optional downstream air classifier.
However, it appears beneficial to apply the vibrating mill in grinding circuits without an air classifier by increasing the retention time.
Case study
Application of vibrating mills for grinding of lignite The application of vibrating mills for grinding of lignite shall be presented by an industrial example of RWE Power, the former Rheinbraun company. The coal refining plant Fortuna-Nord in Bergheim is one of three remaining plants of RWE Power.
During the process design phase in the 1970s it became evident that the fine fraction needed to be removed in order to optimize the economic efficiency. For coking two hearthtype furnaces are installed in which the dry lignite is heated on a special plate. In this process the lignite loses its residual water and its gaseous components. This process is run under oxygen deficiency in order to avoid lignite combustion. The volatile components are used for steam generation and the hot carbon is cooled down by water and air for further transportation. With both hearth-type furnaces lignite as well as activated coke can be treated.
The most profitable solution is to remove all fines < 1 mm. The fraction < 0.3 mm can be sold as filter dust whereas the coarser fraction has to be reduced in size first. In order to achieve the fineness of the filter dust RWE Power installed three Gulin-type vibrating mills.
Before installing the vibrating mills, grinding tests were executed. The test results showed that the largest throughput could be reached with a frequency of 1.000 min-1 and when using rods as grinding media. A calculation showed that for the requested throughput of 9 t/h the Gulin type 65U would be required. In 1976 three vibrating mills were installed, with centre feeding and one) minute grinding time, and the actual capacity was even higher than estimated. Subsequently nine more vibrating mills were installed. shows the grinding unit within the plant of Fortuna-Nord.
The feed material is transported via screw conveyor to the silos upstream of the vibrating mills. In this process it becomes obvious how simple grinding occurs by a singlepass circuit and without air classifier.
After installation of the vibrating mills the guaranteed throughput was considerably exceeded.
Due to its low volume and its low air throughput in the grinding cylinders the risk of fire is very low. The up- and downstream aggregates are connected to the vibrating mill in an airtight way, so that the vibrating mill does not cause any dust emissions.
illustrates that the vibrating mill discharge material contains more even fines than the filter dust. After about 5.000 min-1 operating hours only a minor degree of wear of the grinding media and the wear-resistant liners can be detected. The vibrating mill requires very low maintenance.
Nowadays RWE Fortuna Nord processes 3.9 Mill. t/a raw coal, producing the three products: lignite coke, fluidized-bed coal, and lignite dust.
Two vibrating mills P50U with centre feeding are installed for the production of fine lignite coke, used as filter dust and absorber. Nine more vibrating mills P65U with centre feeding are installed to process lignite dust for industrial combustion plants. The fluidized-bed coal is lignite dust of coarser grain size, which is used for the circulated fluidized-bed technique in power plants. By this technique the whole process is made more efficient and environmentally compatible.