Examining a typical cement clinker grinding mill, which can be considered to be representative of all tube mills, the components normally found as follows:
SHELL LINING PLATES
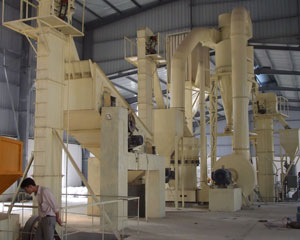
Tubular Grinding Mill
These plates are specially designed and incorporate contour features which inject movement into the ball charge during rotation of the mill. Properties required by the plates vary along the length of the mill.
For instance, at the inlet region of the mill there is likely to be less protection of the plates by ground products and the balls will be of largest size in use and therefore, toughness is of outmost importance. However, along the length of the mill, in second and third chambers, the ball size is considerably smaller and a protective layer of ground material is available and here wear resistance must be at a maximum.
END WALL LINING PLATES
These plates are fitted at the inlet region of the mill and as such are subjected to maximum impact by the large grinding media, therefore, the need to be manufactured in as tough a material as possible whilst at the same time obviously retaining a high degree of wear resistance.
DIAPHRAGM PLATES
Similar comments apply to slotted diaphragm plates particularly those separating first and second grinding chambers because in this region there is frequently a lack of protective ground material as it passes through the slotted plates. It is essential, however, to maintain a high level of hardness in these plates to avoid peening over the slots, thereby reducing mill throughput.
GRINDING BALLS AND CYLPEBS
This item is self-explanatory. Grinding balls vary in size from 12 to 100mm in diameter, the larger balls requiring increased resistance to repeated impact, smaller balls requiring maximum wear resistance. In the case of fine grinding, balls are occasionally replaced by cylpebs which cylindrical products with a height/diameter ratio of unity, the theory being that they posses a higher surface area/volume characteristic than the equivalent diameter grinding balls. Cylpebs are normally produced in sizes ranging from 12×12 to 30×30 mm.
A tubular grinding mill is often used for efficient size reduction application of variety of products such as metallic ores, coal, cement, refractory, pigments and chemicals with the purpose varying from product to product.
Tubular grinding mill application
Cement
The basic raw material for producing cement is a carbonaceous rock called limestone. In addition, other partial substitutes such as blast furnace slag, pozzolanas, fly-ash etc are used for various purposes. The cement manufacturing process involves several stages of size reduction by crushing and grinding, the most critical being the final grinding of clinker after the raw material has been thermally processed in a kiln. This finish grinding operation is most vital as the properties of cement depends, to a large degree, on the particle size which is a controlling parameter for the cement manufacturers.
iron ore
To make best use of low grade iron ores now available worldwide, some type of beneficiation process needs to be carried out to ensure efficient blast furnace operation. Pelletisation is one such process which relies upon the ore being ground to separate the iron bearing particles from the gangue, the ore subsequently being formed into pellets which are sintered prior to the melting operation.
COPPER AND OTHER NON-FERROUS ORES
These metals are normally extracted in the form of very low grade ores, which requires complex processing to extract useful minerals. Initially the metallic ore particles must be physically separated from gangue materials by milling. Subsequent separation is then achieved by a flotation process based on either differential densities or chemical activation.
Coal
Coal is frequently ground for use as pulverized fuel, the most common application being power generation. This is an operation which is sometimes carried out by ball milling, but it is also a field in which a vertical spindle mill is predominant.