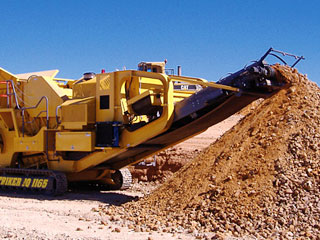
Grind ability of the Ball Mill
Ball mill is vital equipment in industries viz. mineral dressing, ore processing, fertilizers, food and diary, pharmaceuticals and many others. The present work involves a meticulous study of the effect of the various parameters on the performance of a ball mill. The parameters studied in this work are particle size, number of balls, time of grinding, particle density, and speed of the ball mill (rpm). An attempt has been made to develop correlation for the performance of the ball mill by correlating these variables with the grindability on the basis of dimensional analysis approach as well as fractional factorial design method. It is observed that these parameters influence the performance of the ball mill significantly. The performance of a ball mill is measured with reference to the quantity of undersize or fines (amount of grounded material passing through120 mesh screen) per revolution of the mill, collected for variation of each of the individual parameters.
Finally the calculated values of the fines in terms of the grindability of the mill obtained through the correlations by both the above-mentioned methods are compared with the experimental values thereby justifying the analysis with reasonable deviations. Thus the developed correlations can be applied to know the grindability of the Ball Mill over a wide range of parameters.
Grindability, Ball mil, Dimensional Analysis approach, and Fractional Factorial Design
Introduction
In almost all the metallurgical processes, crushing/grinding is considered to be an inseparable unit operation which is adopted at the very first stage of a series of other unit operations and/or unit processes. Size reduction of solids is done almost invariably. Ball mill finds its application in many industries like abrasives, animal products, brewing industry, chemical, confectionery, food processing, fuel preparation, metal powder, mineral preparation, paint preparation, paper, pigments for color industry, abrasives for grinding, plastics, printing ink, rubber, textiles, sintering, cement and limestone, powders for the detergent industry, pulverized coal for power generation, refractory materials for investment casting, dry powder opacifiers for ceramics industry, pharmaceuticals, mineral preparation, refractory materials for investment casting, tungsten powder and dry lubricants, carbon black for rubber, charcoal for briquetting and others.
Mainly because of their simple construction and application ball milling is a wide spread milling technology, particularly in mining. Various parameters viz. particle size, number of balls, time of grinding, particle density and speed of the ball mill (rpm) have been considered for the present work to determine the performance of the ball mill.
Literature
Ball mills are cylindrical or conical shell rotating about a horizontal axis, partially filled with a grinding medium such as natural flint pebbles, ceramic pellets or metallic balls. The common classification of ball mill is any type of mill in which mild steel or iron balls are used. In most cases the cylinder of such mill is made of alloy steel or some special type of lining. The material to be ground is added so that it is slightly more than fills of the voids between the balls (with a maximum limit of number of balls not exceeding 50% of the mill capacity for proper grinding). The shell is rotated at a speed, which will cause the pellets to cascade, thus reducing particle sizes by impact. It has been proposed that in the plastics industry the term ball mill be reserved for metallic grinding media, and the term pebble mill for non-metallic grinding media. There are two different methods of comminution: autogeneous comminution where the material is pure and heterogeneous comminution where the material is mixed with heavy spheres from steel of typical diameter of several centimeters to increase efficiency. There exists much experimental knowledge on the operation mechanism of ball mills and on the comminution of granular matter in these mills. To increase efficiency of the mill one would have to tune the rotation velocity so that the average collision velocity becomes maximum. In this context attempt has been made for a meticulous study of the effect of the various system parameters on the performance of ball mills.
Factors Affecting Size of Product from Ball Mill
It is important to fix the point where the charge, as it is carried upward, breaks away from the periphery of the Mill. This is called as “break point” or “angle of break” because it is measured in degrees. It is measured up the periphery of the Mill from the horizontal [8]. There are four factors affecting the angle of break:
- Speed of Mill
- Amount of grinding media
- Amount of material
- Consistency or viscosity (for wet grinding)
Fractional Factorial Design:
Full and fractional Factorial Design analysis is common in designed experiments for engineering and scientific applications. In many cases, it is required to consider the factors affecting the production process at two levels. The experimenter would like to determine whether any of these changes affect the results of the production process. The most intuitive approach to study these factors would be to vary the factors of interest in a full factorial design, that is, to try all possible combinations of settings.
In statistics, fractional factorial designs are experimental designs consisting of a carefully chosen subset (fraction) of the experimental runs of a full factorial design. The subset is chosen so as to exploit the sparsity-of-effects principle to expose information about the most important features of the problem studied, while using a fraction of the effort of a full factorial design in terms of experimental runs and resources.
Experimental
A ball mill of 36.6 cm diameter and 50 cm length has been used in the laboratory for experimentation. The material of construction of the grinding media used is mild steel. The steel balls each of size 5.41 cm in diameter and density 7.85kg/m3 were selected for the experiments. The mill was made to revolve at different speeds to grind various materials like dolomite, manganese, iron ore, and limestone. Exhaustive study was carried out with the dolomite material. The various system parameters (viz. particle size, material density, speed of the mill, time of grinding and the number of balls) were considered to study their effects on the performance of the ball mill. Scope of the experiment is given in Table 1 and the experimental set up is shown in Fig. 1. The amounts of undersize or fine were found out by sieving with the 120-mesh screen. Each time 1.0 kg of material was taken as feed material for running the ball mill.
Discussion
The critical speed of the ball mill was calculated to be 76rpm. It is observed that the grindability of the ball mill or in other words the amount of fines increase with respect to the overall effect of increase in number of balls, time of grinding, speed (rpm) of the ball mill. But with increase in particle size and particle density the grindability of the mill decreases; whereas it increases with the increase in speed of the ball mill, time of grinding and the number of balls. Therefore the grinding is not so satisfactory for high density particles like iron ores. The equations obtained are in accordance with the experimental observations. From the above expressions it is clear that the factor, which affects the most, is the speed. So for optimizing the grinding process, as compared to other parameters speed has to be controlled to a maximum extent. The effect of various system parameters on grindability has been shown in Fig. 2. The calculated values of the grindability from both the approaches obtained through the developed correlations have been compared with the respective experimental values with mean and standard deviations of -4.38 and 18.75 for D.A.-approach and 3.54 and 11.56 for the F.F.D.-approach respectively as shown in Fig. 3. It is found that the calculated values agree well with the experimental values.