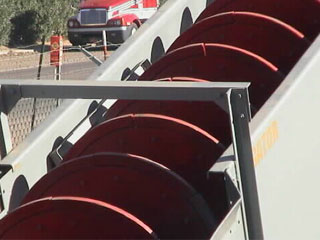
Aggregate Washer Machine
The production of crushed-stone aggregate involves:
Drilling -> Blasting -> Loading -> Transporting -> Crushing -> Screening -> Product handling and storage
In operating a quarry and crushing plant, the drilling pattern, the amount of explosives, the size shovel or loader used to load the stone, and the size of the primary crusher should be coordinated to assure that all stone from the quarry can be economically utilized.
TYPES OF CRUSHERS
Crushers are classified according to the stage of crushing which they accomplish, such as:
1) Primary; 2) Secondary; 3)Tertiary;
- A primary crusher receives the stone directly from a quarry after blasting, and produces the first reduction in size.
- The output of the primary crusher is fed to a secondary crusher, which further reduces the stone size. Some of the stone may pass through four or more crushers before it is reduced to the desired size.
- The degree of breakage is spread over several stages as a means of closely controlling product size and limiting waste material.
- As stone passes through a crusher, the reduction in size may be expressed as reduction ratio.
- The reduction ratio is the ratio of crusher feed size to product size. The sizes are usually defined as the 80% passing size of the cumulative size distribution.
- For jaw crusher, the ratio can be estimated by the gape.
- The gape is the distance between the fixed and moving faces at the top, divided by the distance of the open-side setting at the bottom.
- The reduction ratio of a roller crusher can be estimated as the ratio of the dimension of the largest stone that can be nipped by the roller, divided by the setting of the rolls, which is the smallest distance between the faces of the rolls.
- Crushers are also classified by their method of mechanically transmitted fracturing energy to the rock. Jaw, gyratory, and roll crushers work by applying compressive force. Impact crushers such as single rotor and hammer mill apply high-speed impact force to accomplish fracturing
JAW CRUSHERS
- Jaw crushers operate by allowing stone to flow into the space between two jaws,one of which is stationary while the other is movable.
- The distance between the jaws diminishes as the stone travels downward under the effect of gravity and the motion of the movable jaw,until the stone ultimately passes through the lower opening.
- Jaw crushers are usually designed with the toggle as the weakest part.The toggle will break if the machine encounters an uncrushable object or is subjected to overload.This limits damage to the crusher.
- In selecting a jaw crusher, consideration must be given to the size of the feed stone.
GYRATORY CRUSHERS
- Gyratory crushers are characterized by a gyrating mantle mounted within a deep bowl.
- Gyratory crushers provide continuous crushing action and are used for both primary and secondary crushing of hard,tough, abrasive rock.
GYRATORY STANDARD CONE CRUSHER
- Cone crushers are used as secondary or tertiary crushers.
- Cone crushers are capable of producing large quantities of uniformly fine crushed stone.
- A cone crusher differs from a true gyratory crusher in the following respects:
- 1.It has a shorter cone.
- 2.It has a smaller receiving opening.
- 3.It rotates at a higher speed,about twice that of a true gyratory
- 4.It produces a more uniformly sized stone.
ROLL CRUSHERS
- Roll crushers are used for producing additional reductions in the sizes of stone after the output of a quarry has been subjected to one or more stages of prior crushing.
- A roll crusher consists of a heavy cast- iron frame equipped with either one or more hard-steel rolls,each mounted on a separate horizontal shaft.